Technology plays a vital role in helping businesses improve efficiency, cut costs, and remain competitive. One of the most important innovations in industrial automation is the Programmable Logic Controller (PLC). PLCs can help streamline operations and boost productivity. By integrating PLC components into automated systems, businesses can achieve precise control over machinery.
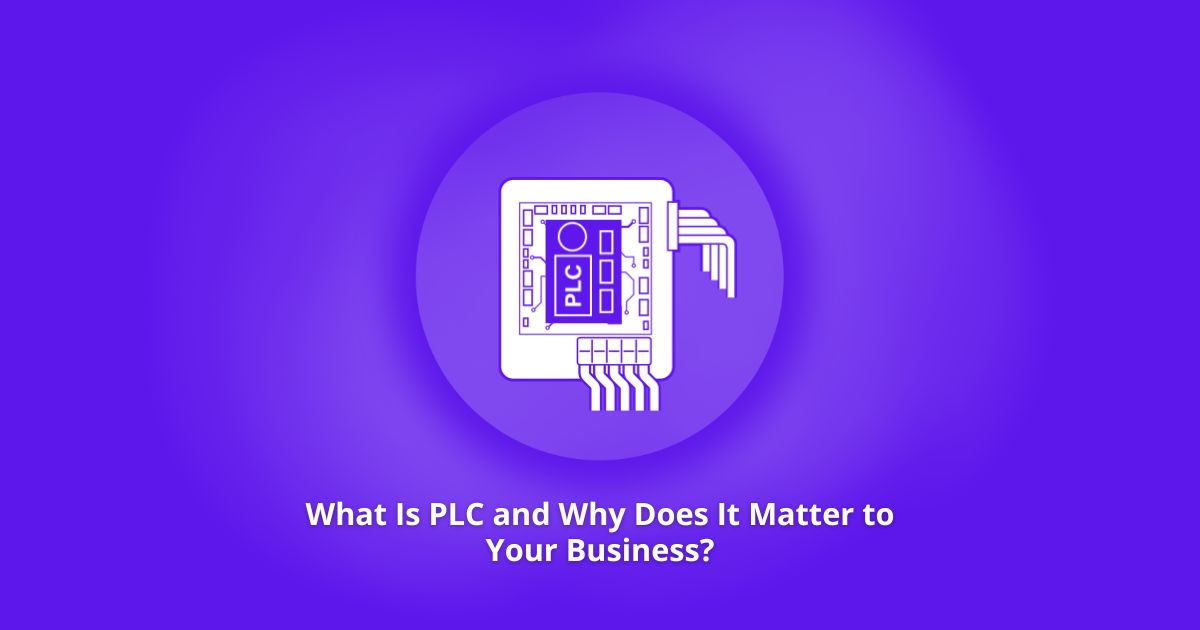
What Is a PLC?
A PLC is a highly specialized industrial computer designed to manage and control machines, production lines, and other automated systems. Unlike traditional computers, PLCs are engineered to endure the challenging conditions of industrial environments, including extreme temperatures, moisture, dust, and vibrations. They play a key role in automation by executing programmed instructions that allow machines to function efficiently with minimal human involvement.
A PLC consists of three main components: a central processing unit (CPU), input/output (I/O) modules, and a programming device. The CPU processes data and executes instructions, ensuring machines function as expected. I/O modules connect the PLC to sensors, motors, and other devices. The programming device is used to write and update the PLC’s control instructions, allowing operators to make changes as needed without extensive rewiring or hardware adjustments.
How PLCs Work?
PLCs operate by following a cyclic process known as a scan cycle. The cycle begins when the PLC collects data from connected devices such as sensors and switches. The CPU then analyzes this input data based on pre-programmed logic. After processing the data, the PLC sends signals to output devices like motors, lights, and alarms. This cycle repeats continuously, ensuring smooth automation of operations.
Different programming languages are used for PLCs, including ladder logic, function block diagrams, and structured text. The choice of programming method depends on the complexity of the task and the specific requirements of the system. Ladder logic is one of the most common programming languages, resembling electrical relay logic, making it easier for engineers with an electrical background to work with PLCs. Function block diagrams provide a graphical approach to programming. Structured text, on the other hand, uses high-level programming concepts.
The reliability of PLCs lies in their ability to process data in real time. As soon as a sensor detects a change in the system, the PLC reacts instantly. This responsiveness is particularly important in industries where timing and precision are crucial, such as manufacturing and process automation.
Why PLCs Matter to Your Business?
PLCs bring significant benefits to businesses across different industries. Here’s why they matter:
1. Improved Efficiency and Productivity
Automation eliminates the need for manual operation, reducing human errors and increasing consistency. Machines controlled by PLCs work faster and more precisely. This allows businesses to meet higher production demands without the need for additional labor.
2. Cost Savings
Although PLCs require an initial investment, they reduce long-term costs by lowering labor expenses, minimizing waste, and preventing machine breakdowns. Automated processes also save energy and reduce material waste. Companies can achieve a higher return on investment by implementing PLCs, as they enable better resource management and lower maintenance costs.
3. Flexibility and Scalability
Unlike traditional hard-wired systems, PLCs can be easily reprogrammed to accommodate changes in production needs. Businesses can update processes without investing in new machinery. If production requirements change, PLCs can be reconfigured to adapt to new workflows.
4. Enhanced Safety
PLCs monitor operations in real-time and can shut down equipment when necessary to prevent accidents. This reduces workplace hazards and ensures compliance with safety regulations. Many PLCs include built-in safety features, such as emergency stop functions, fault detection, and alarm notifications.
5. Remote Monitoring and Control
Many modern PLCs support remote access, allowing engineers and managers to monitor and control systems from anywhere. This feature is especially useful for businesses with multiple locations or large-scale operations. With remote connectivity, technicians can troubleshoot and adjust system parameters without being physically present on-site.
Industries That Benefit from PLCs
PLCs are widely used in industries where automation is essential. Manufacturing companies use PLCs to automate assembly lines, control robotic arms, and manage material handling. The automotive sector relies on PLCs for welding machines, conveyor belts, and precision tasks.
In the food and beverage industry, PLCs help control processing equipment and maintain consistent product quality. Energy and utility companies use PLCs to monitor power distribution, water treatment, and environmental controls. Logistics and warehousing businesses implement PLCs to coordinate conveyor systems and track inventory efficiently.
Choosing the Right PLC for Your Business
Selecting the right PLC depends on the specific needs of your business. Processing power is an important factor, as the PLC must have a CPU capable of handling all necessary applications. The I/O capacity should match the number of input and output devices required for your operations. Communication capabilities play a role in ensuring that the PLC integrates smoothly with your existing systems and network. If your workplace involves extreme conditions, choosing a rugged PLC designed for harsh environments is essential. Businesses anticipating growth should opt for a PLC that allows for future expansion and scalability.
Understanding the workload and complexity of your operations is key when selecting a PLC. Some businesses may require a simple PLC for basic automation tasks, while others may need high-performance PLCs capable of handling complex processes. Consulting with an automation expert can help determine the best PLC for your specific needs.
Common Misconceptions About PLCs
1. PLCs Are Only for Large Businesses
Small and medium-sized businesses can also benefit from PLCs. Many affordable options exist, making automation accessible to companies of all sizes. PLCs can be tailored to meet the needs of smaller operations.
2. PLCs Are Difficult to Program
Modern PLCs come with user-friendly software that simplifies programming. Some even offer drag-and-drop interfaces that require minimal coding knowledge. Training resources and online courses are widely available, making it easier for employees to learn PLC programming and maintenance.
3. PLCs Are Obsolete
While new automation technologies exist, PLCs remain a reliable and widely used solution. They continue to evolve with advancements in networking and remote access capabilities. As industries move toward Industry 4.0, PLCs are incorporating new technologies such as artificial intelligence and cloud computing.
The Future of PLCs
PLCs are becoming more advanced. Future PLCs will integrate more with cloud computing, artificial intelligence, and predictive maintenance tools. This evolution will further enhance automation, efficiency, and decision-making for businesses. Companies that invest in PLC technology today will be better positioned for future advancements in automation and digital transformation.
Conclusion
PLCs are a valuable asset for businesses looking to automate processes, improve efficiency, and reduce costs. Whether you run a manufacturing plant, a warehouse, or an energy facility, integrating PLCs into your operations can provide long-term benefits. PLCs will continue to play a key role in industrial automation.